Developing pharmaceutical and nutraceutical products like tablets and capsules comes with several challenges. Each formulation must be optimized based on the active ingredient’s properties, the type of excipients used, and the manufacturing process. Many formulation issues can lead to production delays, increased costs, and compromised product quality. Based on industry experience, here are five common problems encountered in solid dose formulation and their practical solutions.
Sticky Formulations
Stickiness is one of the most common issues in tablet and capsule manufacturing, where the formulation adheres to the machine’s tooling or capsule-filling components. This can cause:
- Product buildup on punch surfaces.
- Tablets sticking to dies, leading to defects.
- Inconsistent capsule weights and broken capsules.
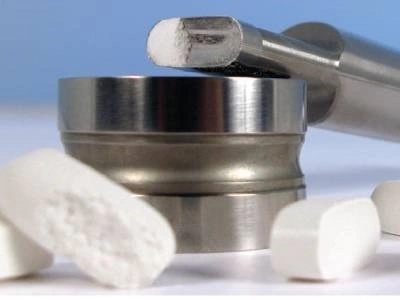
Solutions:
- Add a lubricant such as magnesium stearate or stearic acid to improve powder flow and reduce sticking.
- Control environmental conditions by keeping humidity low and maintaining a temperature between 65°F – 75°F to prevent moisture-related stickiness.
- Regularly clean and maintain equipment to minimize product accumulation.
Poor Flowability of the Powder
The powder formulation must flow smoothly for successful tablet compression and capsule filling. Poor flow properties can lead to:
- Inconsistent tablet weights and dosages.
- Sticking or clogging of the machine.
- Soft or defective tablets.
Solutions:
- Use flow enhancers such as dicalcium phosphate, which adds texture and improves flow.
- Add magnesium stearate as a dry lubricant to reduce friction.
- Granulation (either wet or dry) can improve particle size distribution, reducing the presence of fine powders that cause flow issues.
Poor Solubility of the Formulation
The solubility of a powder mix directly affects the bioavailability and effectiveness of the final product. Some active pharmaceutical ingredients (APIs) are poorly soluble, leading to:
- Reduced absorption and efficacy.
- The need for higher dosages increases production costs.
- Potential side effects due to increased API concentration.
Solutions:
- Capsules (both hard and soft gelatin) can improve the dispersibility of poorly soluble APIs.
- Use hydrophilic binders such as polyvinyl pyrrolidone (PVP), polyethylene glycol (PEG), or starch derivatives to enhance solubility.
- Consider solid dispersion techniques where the API is incorporated into a soluble carrier.
Abrasive Formulations Causing Machine Wear
Some formulations contain coarse, abrasive particles, which can cause excessive wear on tooling, leading to:
- Shorter lifespan of tablet press punches and capsule-filling components.
- Increased machine maintenance and downtime.
- Defects such as lamination, picking, and sticking.
Solutions:
- Use high-durability tooling materials such as high-carbon, high-chrome, or cold-work tool steel to withstand abrasive formulations.
- Apply coatings (e.g., hard chromium) on punches and dies to reduce wear.
- Modify tablet designs to have simpler punch tip shapes that minimize stress on the tooling.
Sensitivity to Environmental Conditions
Some ingredients are highly sensitive to environmental factors like temperature, humidity, and light, which can affect stability and lead to:
- Changes in formulation properties over time.
- Poor binding, resulting in weak tablets or inconsistent capsule filling.
- Degradation of the active ingredient reduces potency.
Solutions:
- Store formulations properly: Keep them away from direct light and maintain a temperature of 65°F – 75°F with humidity between 35% – 65%.
- Use moisture-resistant excipients like microcrystalline cellulose, dicalcium phosphate, or silicon dioxide to help maintain stability.
- HPMC capsules (hydroxypropyl methylcellulose) are a good alternative to gelatin capsules as they offer better moisture resistance.
- Apply a protective film coating to tablets to enhance stability.
- Choose appropriate packaging, such as blister packs or sealed containers, to prevent exposure to external conditions.
Conclusion
Developing a solid dose formulation involves overcoming multiple technical challenges, from ensuring good flow properties to maintaining ingredient stability. By incorporating the right excipients, optimizing environmental conditions, and selecting durable tooling, manufacturers can improve product quality and production efficiency. Identifying potential formulation issues early and implementing the right solutions will save time, reduce costs, and enhance product performance.
References:
- Aulton, M. E., & Taylor, K. M. G. (2017). Aulton\’s Pharmaceutics: The Design and Manufacture of Medicines (5th ed.). Elsevier.
- Rowe, R. C., Sheskey, P. J., & Quinn, M. E. (2009). Handbook of Pharmaceutical Excipients (6th ed.). Pharmaceutical Press.
- Kibbe, A. H. (2000). Handbook of Pharmaceutical Excipients (4th ed.). American Pharmaceutical Association.
- Lachman, L., Lieberman, H. A., & Kanig, J. L. (1986). The Theory and Practice of Industrial Pharmacy (3rd ed.). Lea & Febiger.
- European Medicines Agency (EMA). (2017). Guideline on Pharmaceutical Development of Medicines for Oral Administration.
- U.S. Food and Drug Administration (FDA). (2020). Guidance for Industry: SUPAC-MR: Modified Release Solid Oral Dosage Forms.