Pharmaceutical tablet compression is a fundamental process in medicine production. It transforms a blend of ingredients into solid tablets, which are then packaged and distributed to patients. This process is crucial for ensuring the medication’s effectiveness and safety.
Introduction to Tablet Compression
Tablet compression is a vital aspect of pharmaceutical manufacturing. It involves meticulous attention to detail, from ingredient selection to final packaging. Mastering the compression process helps ensure the production of high-quality tablets that meet the necessary standards.
Key Aspects of Tablet Compression
- Tablet compression is essential for consistent and reliable drug delivery.
- The process involves pressing pharmaceutical ingredients into a solid tablet form.
- Various factors, including ingredient properties and equipment settings, influence the final product’s quality.
- Achieving uniformity in size, shape, and composition is crucial.
- Process optimization can enhance tablet quality and production efficiency.
Understanding Tablet Compression
Tablet compression transforms pharmaceutical mixtures into solid, easy-to-handle tablets using specialized machines. The process includes several steps, such as blending, granulation, and compression, each of which contributes to the tablet’s overall efficacy and safety.
Fundamental Aspects:
- Definition: Tablet compression applies controlled pressure to form solid tablets from a powdered mixture.
- Role in Pharmaceutical Manufacturing: It ensures precise and uniform dosage forms.
- Historical Development: Advances in technology have led to more efficient and high-quality production methods.
Steps in Tablet Compression
Step | Description |
Mixing | Combines pharmaceutical ingredients into a homogenous blend. |
Granulation | Forms granules to enhance flow and compressibility. |
Compression | Applies pressure to create solid tablets. |
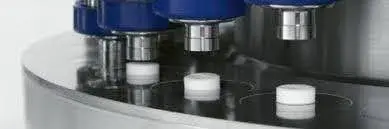
The Science Behind Tablet Compression
The compression process involves applying forces to shape pharmaceutical materials into tablets. Ensuring product quality and meeting regulatory standards requires understanding key physical and chemical properties, including:
- Particle size and distribution – Affects flowability and compressibility.
- Moisture content – Influences binding properties.
- Compression force – Determines tablet density and hardness.
Essential Equipment for Tablet Compression
High-quality tablet compression equipment is crucial in pharmaceutical production. Various components work together to ensure efficiency and consistency:
- Compression tooling (punches and dies): Affects tablet shape and integrity.
- Die tables and feeders: Control the flow of powder into the compression chamber.
- Force control systems: Maintain consistent compression pressure.
Raw Material Considerations
The quality of raw materials significantly impacts tablet formation. Pharmaceutical ingredients, including active components and excipients, must meet strict standards regarding:
- Purity and potency – Ensure therapeutic effectiveness.
- Flow properties – Facilitates smooth manufacturing.
- Moisture content – Prevents degradation and enhances stability.
Pre-Compression Processing
Before compression, materials undergo preparation processes to optimize their properties:
- Granulation (wet or dry) enhances uniformity and flow characteristics.
- Particle size control ensures consistency in dissolution and mechanical strength.
- Moisture regulation prevents caking or clumping.
Advances in Tablet Compression Technology
Modern technology has revolutionized tablet manufacturing, improving efficiency and compliance:
- Automated systems enhance precision and consistency.
- Real-time monitoring ensures adherence to regulatory standards.
- Minimized material waste leads to cost-effective production.
Quality Control in Tablet Compression
Quality control measures ensure tablets meet regulatory standards. Key parameters include:
- Weight variation – Ensures dosage accuracy.
- Hardness testing – Determines durability and dissolution properties.
- Dissolution rates – Ensures proper drug release in the body.
Common Challenges and Solutions
Tablet compression can present challenges, such as:
Challenge | Cause | Solution |
Capping & Lamination | Improper compression force | Adjust pressure settings & material quality |
Hardness Variability | Inconsistent raw materials | Implement strict quality checks |
Equipment Malfunctions | Poor maintenance | Regular servicing & calibration |
Regulatory Compliance & Documentation
Pharmaceutical manufacturers must adhere to Good Manufacturing Practices (GMP) to ensure product safety. Key requirements include:
- Validation protocols – Confirm process consistency.
- Detailed record-keeping – Ensures traceability.
- Quality assurance systems – Maintain high production standards.
Optimization Strategies
To enhance tablet compression efficiency, manufacturers employ:
- Design of Experiments (DOE) – Identifies key factors influencing tablet quality.
- Statistical Process Control (SPC) – Monitors and controls process variations.
- Ingredient & equipment adjustments – Optimize formulation and production settings.
The Future of Tablet Compression
Innovations in materials and technology will continue to shape the future of tablet manufacturing, leading to:
- Enhanced automation for improved precision.
- New formulation techniques for better drug delivery.
- Stronger regulatory integration to ensure global compliance.
Conclusion
Tablet compression is a cornerstone of pharmaceutical production, requiring precise control, advanced technology, and rigorous quality assurance. As the industry evolves, continuous improvements in materials and processes will lead to safer, more effective medicines.
References
- Aulton, M. E. (2018). Pharmaceutics: The Design and Manufacture of Medicines. Churchill Livingstone.
- Lieberman, H. A., Lachman, L., & Schwartz, J. B. (2020). Pharmaceutical Dosage Forms: Tablets. CRC Press.
- European Medicines Agency (EMA). (2022). \”Good Manufacturing Practices (GMP) Guidelines.\”
- U.S. Food and Drug Administration (FDA). (2021). \”Pharmaceutical Quality Standards.\”