Objective
This case study will discuss the mix-up event of Pyrimethamine with an isosorbide mononitrate tablet. The incident converted into an accident leading to multiple casualties and adverse events. The objective of this case study is to relate the incident with the 12 essentials of GMP and how the violation of these essentials led to the severe adverse event.
Introduction to the case study
A renowned pharmaceutical company, whose facility was GMP-approved by regulatory authorities, and was the manufacturer of several generic products and multiple dosage forms.
A product, Isosorbide mononitrate 20 mg is manufactured by this reputed pharmaceutical organization. Isosorbide mononitrate was manufactured and supplied to multiple pharmacies for the treatment of angina symptoms. Many batches of this product had already been supplied to the market, the product was approved, and this had already gone through the phase of validation and stability studies.
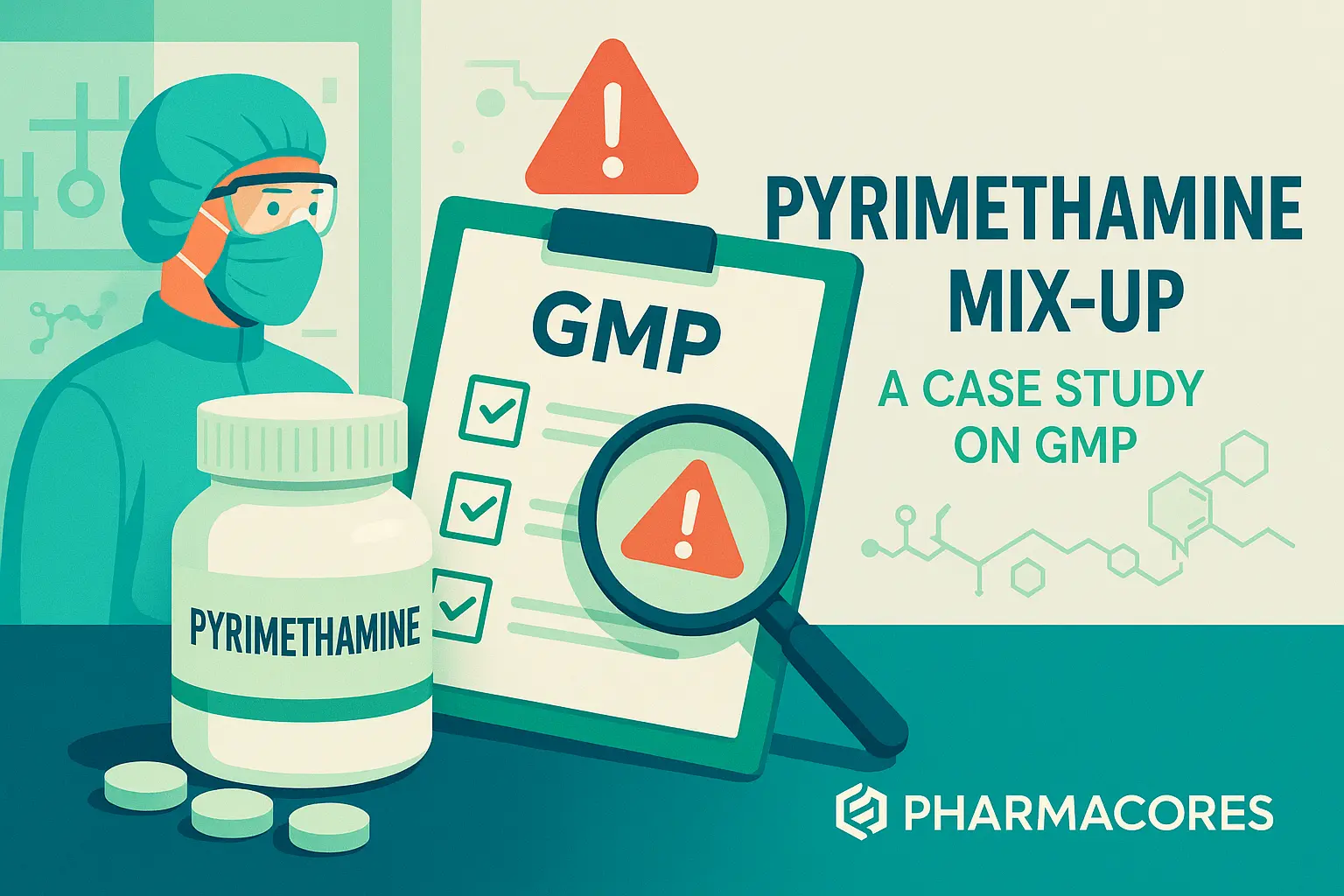
Product Consumption
The incident took place in 2012. The drug product was manufactured successfully and sent to the Pharmacy for patient consumption after quality control released the product. The product was supplied to a reputed pharmacy and a Hospital.
Around thousands of patients took this medication, and around 213 casualties were observed. 1000 patients felt ill but survived.
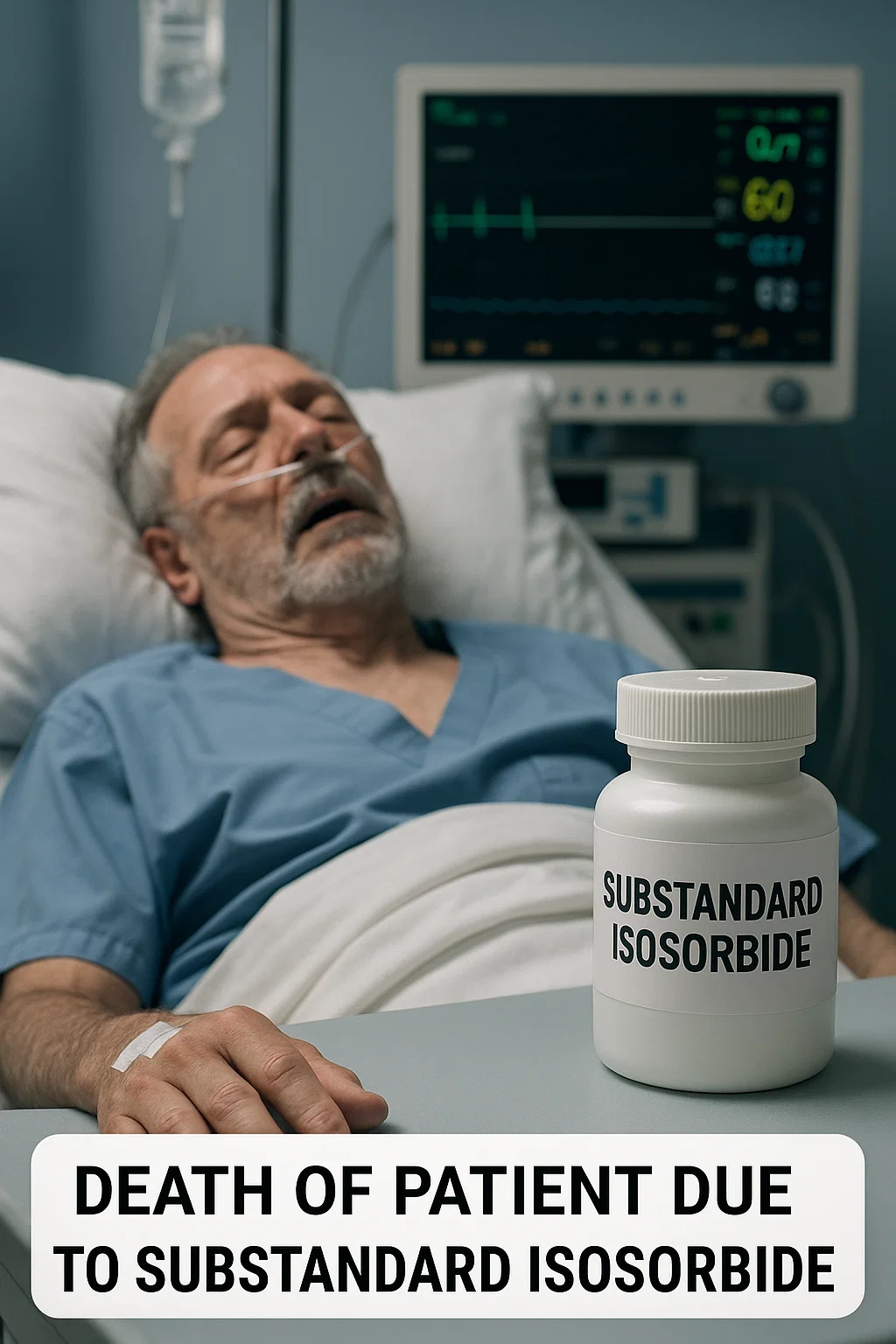
Symptoms of the product
Patients who consumed this Isosorbide mononitrate 20 mg molecule observed the following symptoms and were admitted to the hospital. Some of the patients recovered, and some of the patients died due to the symptoms worsening.
- Bone marrow suppression
- Darkening of the skin
- Lower WBCs
- Excessive Bleeding
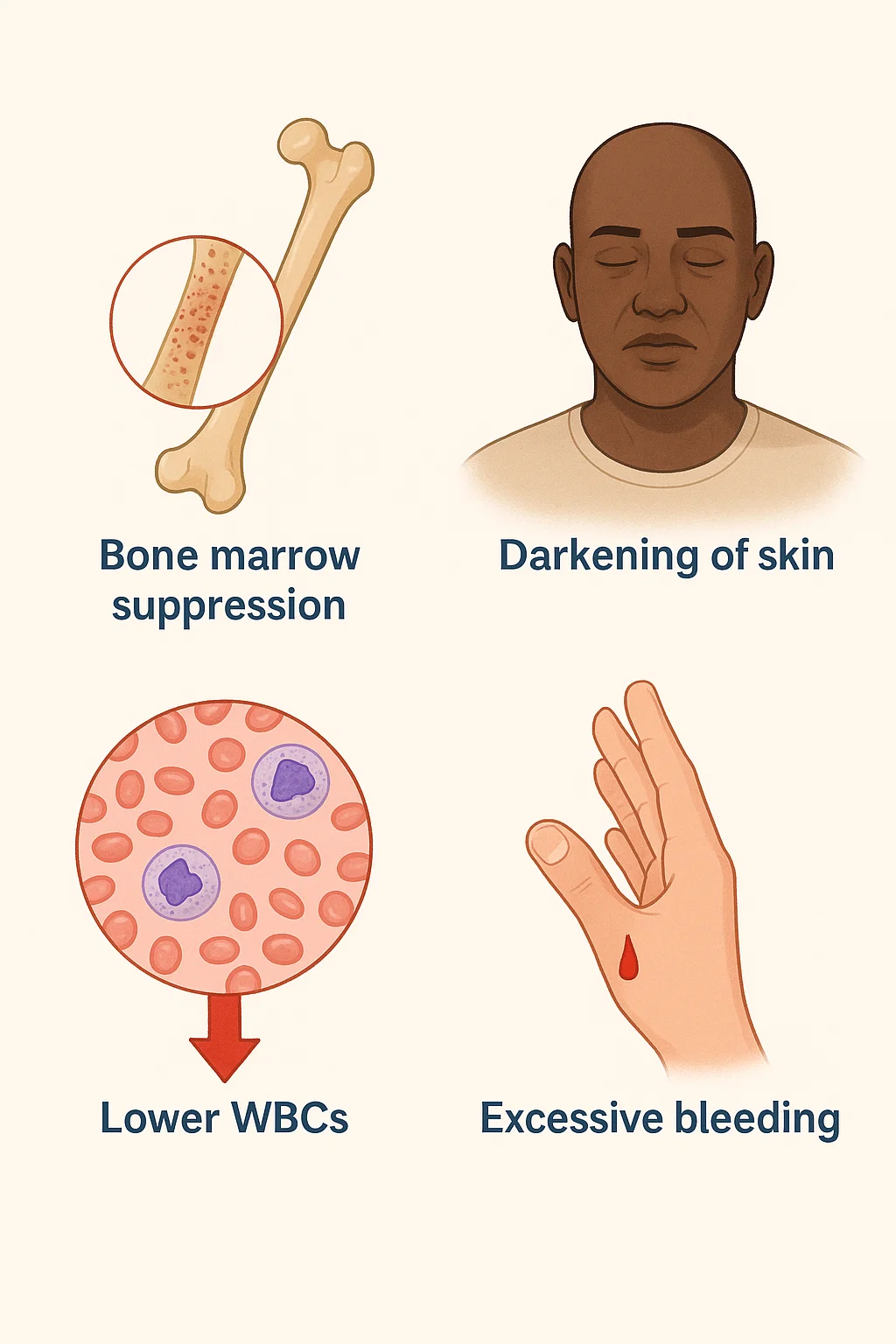
Around 9.2 million tablets were seized by the regulatory authority due to unforeseen conditions. 9.2 million tablets were comprised of 23 batches, which were supplied to the hospital and pharmacy.
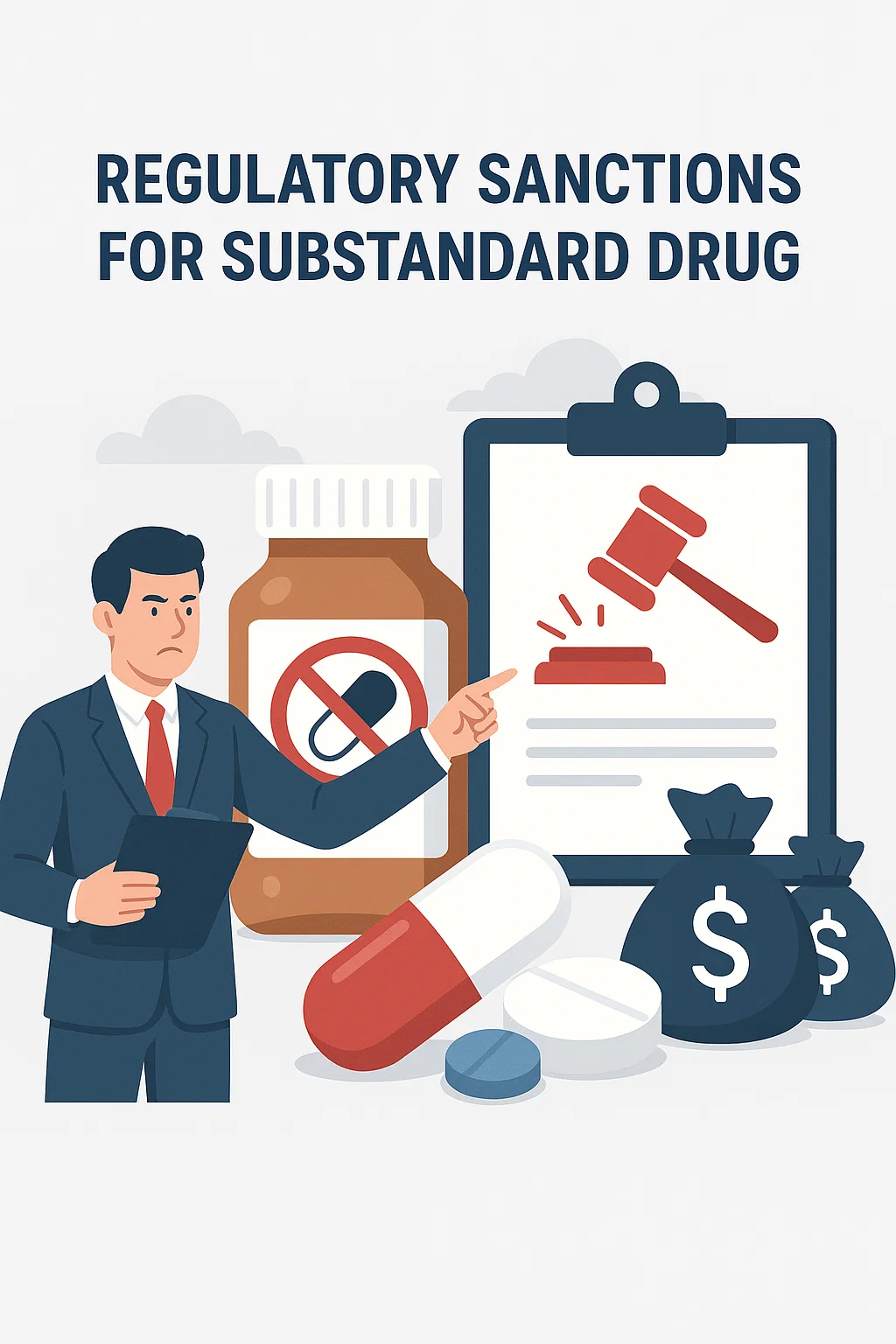
Adverse Event and Test Reports
Upon receiving severe symptoms and deaths in the patient, this product was immediately held by government officials and sent for testing by a local laboratory and the London Laboratory. In the meantime, operations of the said pharmaceutical were halted by the regulatory authorities, and the raw material, pyrimethamine.
The results of the Isosorbide mononitrate 20 mg were issued by government officials stating that the product Isosorbide mononitrate 20 mg is contaminated with pyrimethamine and is considered a substandard product.
All the stock was seized and rejected.
Potential Causes of Failure
The product was found to have failed as it violated the GMP essentials. What could happen that leads to product failure?
Personal:
Following are the assumptions related to the personal.
- A person is not qualified to perform the dispensing operation.
- Persons are not qualified for the quality control test of the product.
- Personal behavior was non-serious during the operation from dispensing till the end of tableting.

Dispensing Operation
Before the dispensing operation store pharmacist must check the raw materials as per the list mentioned in the batch shop order. Each container would be checked before entering the dispensing.
Checks before dispensing include the name of the material, lot, release status, and expiry date of the said lot, with the respective shop order of the batch. QA Pharmacist will verify the check and allow the material in the dispensary for weighing as per the shop order and BOM. It may be assumed that the check has not been done in case of contamination of pyremethamine with Isosorbide mononitrate 20 mg.
Production Operations
Soon after the dispensing batch was ready for manufacturing. Raw materials were identifiable due to their Physical appearance, Smell, and Particle size. Some of the raw materials are not identifiable.
Some characteristics of both molecules are,
Characteristics | Pyrimethamine | Isosorbide mononitrate 20 mg |
---|---|---|
Physical appearance | Solid | Crystalline powder |
Color | White to off white | White |
Odor | Odorless | Odorless |
Taste | Bitter | Slightly Bitter |
UV wavelength | 270-275nm | 210-220 nm |
Retention Time | 6-10 min | 2-5 min |
Sample | Tablet | Tablet |
Major ignorance is observed at the time of dispensing and manufacturing. There is the possibility that pyrimethamine was dispensed instead of any excipient, i.e., lactose or avicel.
The accident took place due to the adverse effect of pyrimethamine found in higher proportions in the isosorbide mononitrate tablet.
The contamination of the said product could not have happened at the production stage, which caused casualties, because the source of contamination in production areas would be equipment, utensils, and empty containers. The aforementioned source could not contain higher amounts of pyrimethamine.
Let’s consider an example,
If it is to be assumed that equipment was not properly cleaned it means equipment will carry a minimum amount of proportion of pyrimethamine that could cause contamination but this quantity is not able to produce significant adverse symptoms.
Mix Up Scenerio 1:
Assume you are producing a 20 mg isosorbide mononitrate tablet and the batch size is 400000 tablets around 80 kg. The average weight of a tablet is 200 mg.
Assume that the equipment was not properly cleaned and contains 1 kg of pyremethamine powder in a High shear mixer. What would happen? 1 kg of pyrimethamine in 80 kg. It means an isosorbide mononitrate tablet contains around 2.5 mg of pyrimethamine in this scenario. This is not the toxic dose at all. It means this is not the case of contamination that led to death and severe adverse symptoms.
Mix Up Scenerio 2:
Assume you are producing a 20 mg tablet isosorbide mononitrate, and the batch size is 400000 tablets, around 80 kg. The average weight of a tablet is 200 mg.
The pharmacist received two batches early morning for manufacturing from dispensing. One is of pyrimethamine and the other is of isosorbide mononitrate, and he is in a hurry to manufacture. He kept both batches on a single platform and mistakenly status labels of lactose for Isosorbide mononitrate, and the status label of pyrimethamine fell down on the floor. He confused and mistakenly placed the wrong labels on these two ingredients. The batch was manufactured and contained a higher proportion of pyrimethamine.
Consider the Batch size of the pyrimethamine tablet was 800000 tablets, and around 160 kg. This batch size of 160 kg contains 20 kg of pyrimethamine which will produce pyrimethamine containing 25 mg per tablet.
Let’s assume,
The lactose quantity was 20 kg for isosorbide mononitrate replaced with pyrimethamine, so the quantity of pyrimethamine per tablet would be 50 mg. This is toxic for angina patients, leading to severe adverse effects and death.
What is the Toxic dose of Pyrimethamine? The toxic dose of Pyrimethamine is more than 120mg -200 mg per day in adults. However, the daily required dose of isosorbide may vary depending on the angina symptoms. It may vary from 10-40 mg and 2 to 3 times daily.
The required dose of Pyrimethamine is 50 to 75 mg daily.
It is assumed that those who consumed isosorbide mononitrate 20 mg more than 75 mg a day got adverse symptoms and those with severe conditions did not tolerate the symptoms and died.
It has also been assumed that it might be dispensed wrongly as an excipient.
Storage Facility
Raw Materials storage is another important aspect of GMP. In the case study, it is assumed that there is no proper segregation between the active ingredients and excipients. Warehouse personnel mistakenly brought the wrong container. He might brought a pyrimethamine container instead of lactose or Avicel.
Status Labeling
Certain possibilities violate the GMP practices, some of them are as follows,
- Status labels were not mentioned on the container properly
- Warehouse personnel have placed the wrong label on pyrimethamine.
- There might be a possibility that a loose quantity of pyrimethamine was kept in the excipient drum instead of its original drum due to a loose quantity.
- Warehouse personnel mistakenly placed the bag of pyrimethamine in an empty container bearing the label of lactose or avicel.
These are all possibilities that prevented its identification during the dispensing operation, but here we found a lack of experience. The dispensing operator who performs the dispensing operation is very much aware of the physical appearance of the powders. He is capable of identifying the ingredient by its physical nature. In this case of mix-up, the dispenser was not experienced enough to identify the wrong material.
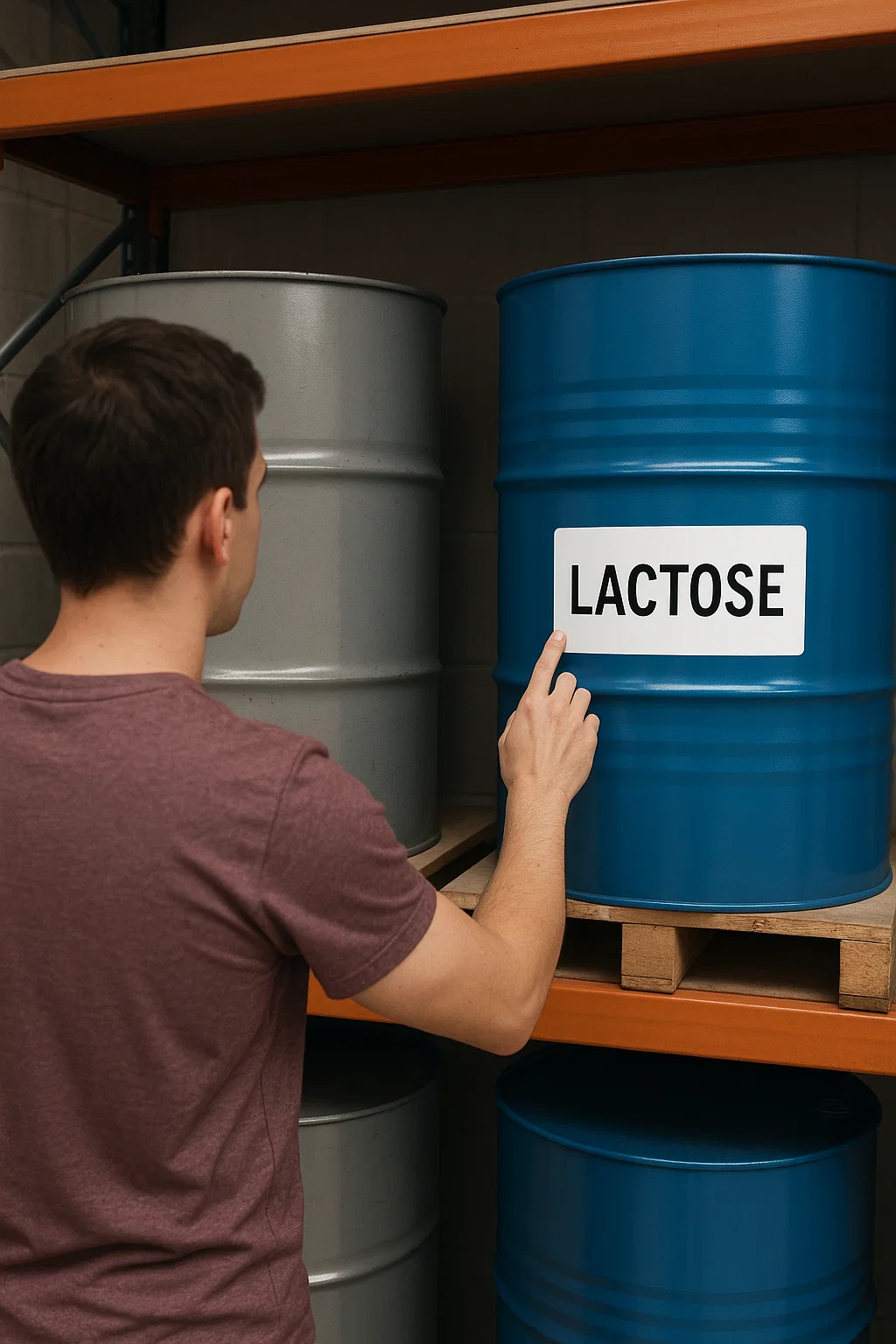
Quality Control
Failure of quality control to identify pyrimethamine during testing of the product. The following are the reasons.
- The wavelength of both isosorbide and pyrimethamine is different.
- The retention times of both molecules are different.
- The product was not identified upon physical checking.
What procedures could identify this?
- Physical stock checking at the raw material store
- It could have been identified during the granulation process because of the nature of the ingredients.
- QC must have been observing the extra peaks that appeared during the testing.
- Peaks of impurities must not be ignored
- Mass spectrometry to identify the peaks
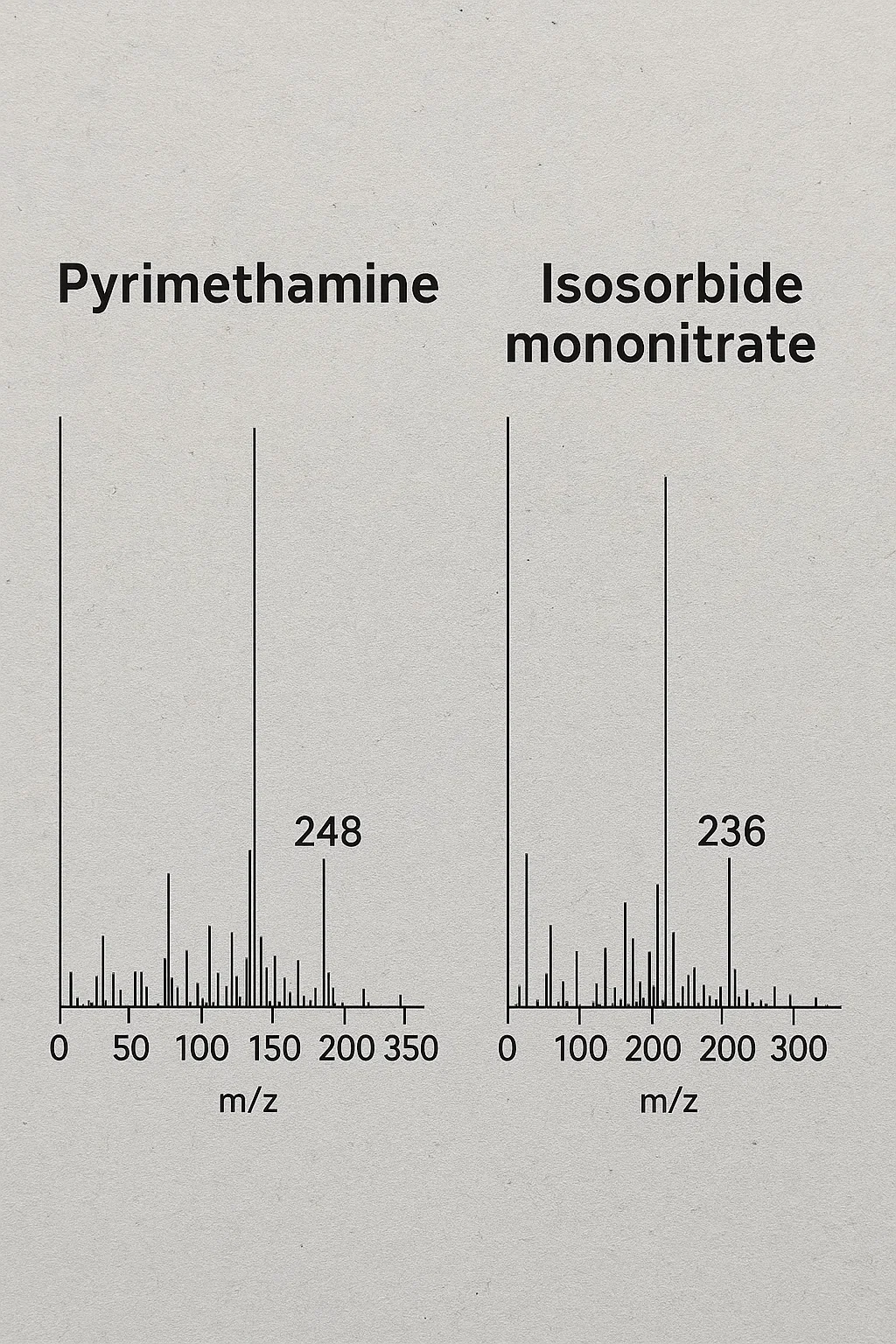
Conclusion
In the case study, we saw that a product containing isosorbide mononitrate was contaminated with pyrimethamine at a much higher level, which caused casualties and adverse reactions in many patients. The root cause is clear and loud: the mismanagement of the product since the start, and the contamination not identified at any stage from the dispensing till the quality assurance product release.
Many stages indicated that something was wrong. The question is why the quality control did not identify the absence of pyrimethamine in another product, which might be manufactured on the same day or maybe the day after the incident. There may have been some suspicious activity that was initially concealed, but the case was investigated by higher authorities, and the culprits were punished afterevidence of their guilt was found.