Introduction:
Process visibility is the difference between managing your operations with a blindfold versus having a clear, 360-degree view of what’s happening across manufacturing, quality, and supply chain processes in real time. In this article, we’ll explore what process visibility truly means in the context of pharmaceutical operations and how to apply it.
What Is Process Visibility?
Process visibility is about transparency within the business processes. It refers to the ability to monitor, track, and analyze operational data across departments, systems, and timeframes to make informed decisions quickly and confidently. Process visibility isn’t just about data; it’s about making that data actionable, accessible, and easy to interpret by those who need it most. When done right, process visibility enables proactive management. It empowers continuous improvement, reduces waste, and ultimately contributes to better patient and business outcomes
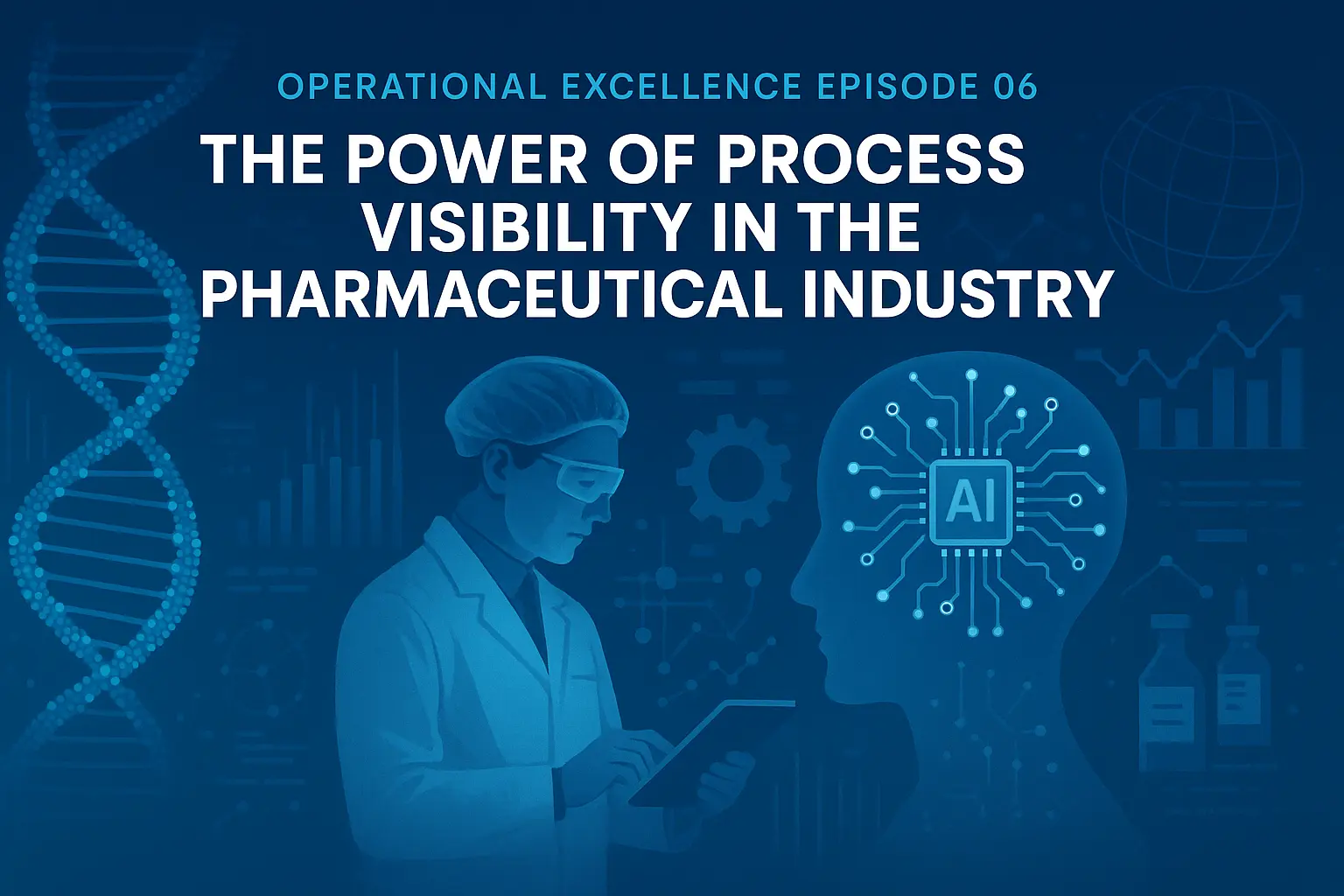
In the pharmaceutical field this means:
- Seeing real-time production data.
- Tracking batch records, deviations, and approvals.
- Monitoring quality metrics.
- Visualizing supply chain and inventory levels.
The Unique Landscape of Pharmaceutical Operations:
Pharmaceutical operations are among the most complex and tightly regulated in the world. Between GMP requirements, regulatory inspections, documentation expectations, and quality assurance, the margin for error is razor thin.
Let’s consider some of the factors that make process visibility essential in pharma:
- Highly regulated environment: Compliance with agencies like the FDA, EMA, and WHO demands meticulous record keeping and traceability.
- Complex manufacturing processes: From raw material testing to secondary packaging, the product journey involves dozens of steps.
- Cross-functional interdependence: Manufacturing can’t proceed without quality department approval; packaging waits on lab release; distribution depends on sales, purchasing orders.
- Batch-based production: One deviation can affect thousands of units and cost millions in reworks or recalls.
Without visibility, issues go unnoticed until it’s too late, leading to batch failures, production downtimes, compliance violations, or worse, patient harm. That’s why making your processes transparent, trackable, and measurable is no longer optional, it’s a competitive and regulatory necessity.
Pillars of Process Visibility:
What does it take to make your operations “visible”? While technology plays a significant role, it’s more than just installing new software. Process visibility rests on several foundational pillars:
A. Real Time Data Collection:
Decisions are no longer based on yesterday’s reports. With sensors, IoT devices, and smart equipment, it’s now possible to gather live data from production, labs, market, and logistics.
B. Digital Integration:
Systems like MES (Manufacturing Execution Systems), ERP (Enterprise Resource Planning), LIMS (Laboratory Information Management Systems), and QMS (Quality Management Systems) must speak to each other. Integration breaks down silos and gives teams a unified view.
C. Visual Management & Dashboards:
Process data should be presented in clear, visual formats like dashboards, KPIs, and trend graphs so that floor workers and top management alike can understand what’s going on instantly.
D. End-to-End Traceability:
From raw materials to finished product, traceability is non-negotiable. Every action, approval, and measurement should be logged and linked to a batch, operator, or device.
E. Communication Channels:
Cross-functional visibility means that QA, manufacturing, supply chain, and engineering can all see and act on shared data without delay. Collaboration platforms and digital workflows help here.
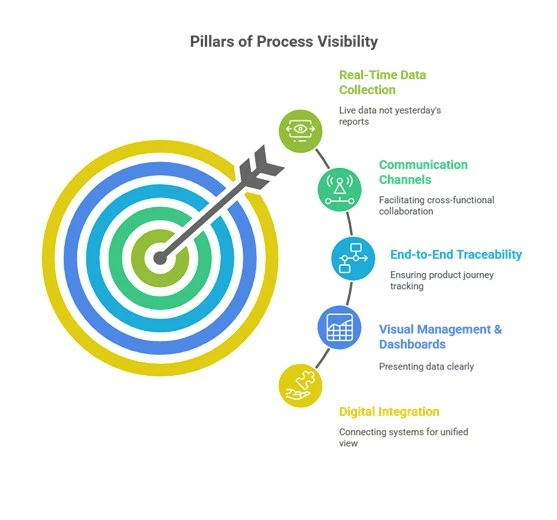
Benefits of Process Visibility in Pharma:
When pharmaceutical companies invest in process visibility, the benefits span on both operational and strategic levels:
1. Enhanced Compliance & Audit Readiness:
Regulatory inspections are less stressful when data is clean, traceable, and instantly retrievable. Visibility enables swift document retrieval, clear batch histories, and transparent analytical and compliance records.
2. Better Root Cause Analysis:
When deviations or failures occur, visibility allows you to analyze process trends, correlate variables, and determine root causes faster, reducing downtime and improving CAPA effectiveness.
3. Proactive Issue Detection:
Early warning signs, such as drifting parameters, equipment wear, or depleted inventory stocks, can be caught before they escalate, minimizing risks and delays.
4. Improved Productivity & Resource Utilization:
When you can see bottlenecks and underused resources in real time, you can take corrective action, whether reallocating resources, adjusting schedules, or reordering materials.
5. Faster Decision-Making:
Whether it’s a yes or no for batch release, or a project greenlight, visibility ensures decisions are based on facts, not assumptions or outdated reports.
6. Smoother Project Execution:
In tech transfers, new product introductions, or equipment upgrades, visibility into timelines, risks, and interdependencies enables smoother execution and fewer surprises.
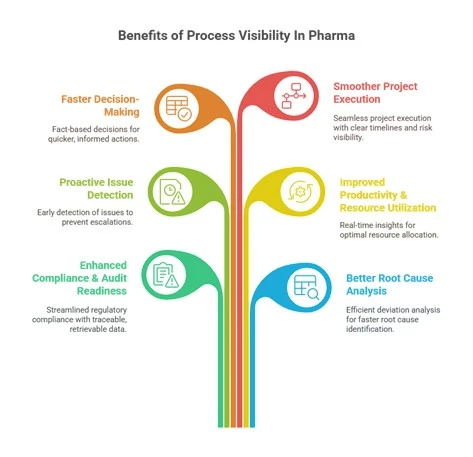
Creating a Culture That Embraces Visibility:
Process visibility isn’t just about installing dashboards, it’s a cultural shift. Employees must feel empowered, not exposed, by transparency. Here’s how to build the right mindset:
1. Leadership Role Modeling:
Executives and managers should lead by example by using data in reviews, asking questions based on facts, and celebrating transparency.
2. Training and Upskilling:
Teams must understand the “why” behind new tools and metrics. Ongoing training helps in overcoming the fear of change and builds confidence in new systems.
3. No-Blame Reporting:
If workers are afraid to report deviations or suggest improvements, visibility fails. Executives and managers must foster a culture where transparency is rewarded, not punished.
4. Collaboration Over Silos:
Encourage cross-functional discussions and collaborative problem solving. When people see how their data affects others, they become more accountable and engaged.
Technology Enablers of Visibility:
The evolution of process visibility has been significantly accelerated by advancements in digital technologies. Successful pharma operations are increasingly using modern tools that enable real-time monitoring, predictive analytics, and integration across departments.
1. MES (Manufacturing Execution Systems):
MES is the backbone of digital manufacturing. It bridges the gap between enterprise-level planning systems (like ERP) and the physical production floor. An MES captures data from machines, operators, and workflows to provide a unified, real-time view of production activities. MES connects production equipment, operators, and quality teams in real time, offering electronic batch records, deviation logging, and step-by-step visibility.
Impact on Visibility: With MES, pharmaceutical companies gain complete transparency into production processes. Operators can follow standard operating procedures (SOPs) with the system flagging deviations instantly. Quality assurance teams can review batch data as it is generated, reducing the time required for batch release. MES integrates with other systems like LIMS, QMS, and ERP, allowing seamless data flow.
2. Internet of Things (IoT) and Smart Devices:
IoT enables the connection of equipment, sensors, and devices to a cloud or enterprise systems, allowing real-time data collection and monitoring. Sensors can monitor temperature, humidity, vibration, flow rates, and more. IoT enables proactive intervention. For example, if a temperature spike is detected in a warehouse, alerts trigger immediate corrective actions. This minimizes product loss and ensures regulatory compliance.
Impact on Visibility: IoT transforms passive assets into active sources of intelligence. Instead of relying on manual logs or delayed reports, teams can access live data dashboards that reflect the current state of every critical parameter.
Implementation Considerations:
- Requires robust cybersecurity protocols.
- Integration with existing automation and SCADA systems.
- Calibration and validation of sensors.
3. AI and Predictive Analytics:
Machine learning models can identify patterns and predict deviations before they happen. They analyze huge data sets to identify patterns, predict outcomes, and recommend actions. In pharma, this translates to smarter, faster, and more accurate decision-making.
Applications:
- Predicting equipment failure to schedule preventive maintenance.
- Forecasting deviations based on historical process data.
- Optimizing production schedules for maximum efficiency.
- Enhancing root cause analysis of quality events.
4. Cloud Platforms:
Cloud-based tools enable global access to data, real-time collaboration, and achievable solutions without heavy infrastructure. When combined with integrated systems architecture, it enables true enterprise-wide visibility. With cloud-based systems, pharma companies can access production data across sites, support remote audits, and collaborate globally. It also facilitates disaster recovery, data backup, and regulatory reporting.
Key Features:
- Centralized data repositories.
- Role-based access and real-time collaboration.
- Seamless integration between ERP, MES, LIMS, and QMS.
- Remote monitoring and control.
Challenges to Achieving Process Visibility:
Despite its benefits, implementing process visibility isn’t without hurdles:
- Legacy Systems: Many pharma manufacturers still rely on paper or isolated systems that aren’t easy to digitize or integrate.
- Data Silos: Different teams often maintain their own spreadsheets or tools, creating fragmented views.
- High Investment Costs: Advanced platforms, sensors, and integration projects can be expensive, especially for smaller manufacturers.
- Change Resistance: People may fear being monitored or blamed, leading to resistance towards visibility.
- Validation Burden: All digital tools must be validated, documented, and compliant with regulations, which can delay rollouts.
Overcoming these challenges requires a phased approach, strong governance, and leadership support.
Roadmap for Implementing Process Visibility:
Ready to start your visibility journey? Here’s a practical step-by-step roadmap:
- Assess Current State: Identify gaps and disconnected processes.
- Define Key Metrics: Choose KPIs that really reflect the processes.
- Select Tools & Partners: Pick scalable, compliant technologies with proven pharma track records.
- Start Small: Pilot in one department or process. Prove value before scaling.
- Train & Engage: Build users’ skills and involve them in design decisions.
- Integrate Systems: Ensure your platforms (MES, LIMS, ERP) talk to each other.
- Review & Improve: Use dashboards and feedback loops to drive continuous improvement.
Process Visibility and the Future of Operational Excellence:
In the journey toward Operational Excellence, visibility isn’t just a supporting tool, it’s a foundation. You can’t improve what you can’t see. With clear insight into how processes behave, where they fail, and how they can improve, organizations can achieve leaner, faster, and more reliable outcomes.
As we move toward Pharma 4.0, where smart factories and AI redefine what’s possible, process visibility will only become more vital. The future belongs to companies that invest in transparency, foster a culture of openness, and empower their teams with real-time insights.
Conclusion:
Operational excellence is a destination reached through many paths, but none can be navigated without visibility. In the pharmaceutical industry, where quality is vital and timelines are tight, knowing what’s happening at every level of your operations can mean the difference between success and failure.
Whether you’re managing a manufacturing plant, overseeing quality, or driving digital transformation, embracing process visibility gives you a powerful advantage. It’s not just about seeing more, it’s about doing more with what you see.
In the end, process visibility is not just a principle. It’s a mindset, a capability, and a strategic advantage. Make your processes visible, and excellence will follow.