This article delves into the critical role of pharmaceutical disintegrants in drug formulation, exploring their function, types, examples, and implementations in various dosage forms. Disintegrants are crucial excipients that promote the quick disintegration of tablets or capsules, aiding in the release and absorption of active pharmaceutical ingredients (APIs).
The article highlights the mechanisms of disintegrant action, including swelling, wicking, and gas production, and provides examples of commonly used disintegrants such as croscarmellose sodium, sodium starch glycolate, and crospovidone. We will also discuss the challenges and advancements in disintegrant technology, such as co-processed excipients and modified-release formulations. When we understand the role of disintegrant, we will realize that pharmaceutical scientists can, in this way, enhance drug delivery systems to optimize bioavailability and patient outcomes.
Pharmaceutical Disintegrant: Function, Examples, and Implementations
They ensure the effectiveness of solid dosage forms, such as tablets and capsules. These excipients are used for the rapid breakup of the dosage form upon administration, allowing the active pharmaceutical ingredient (API) to be released and absorbed by the body. Without disintegrants, tablets would remain intact, delaying drug release and reducing therapeutic effect. We will explore their function, examples, and implementations, highlighting their importance in drug delivery systems.
A- The Function of Disintegrant
They are added to pharmaceutical formulations to stimulate the breakup of solid dosage forms into smaller particles when they come into contact with water or gastrointestinal fluids. This process, known as disintegration, is crucial for ensuring the rapid release of the API, which in turn enhances its bioavailability and therapeutic effect.
Disintegrants achieve this through several mechanisms:
- Swelling:
Examples can be such as starch and croscarmellose sodium, where they absorb water and then swell, creating pressure within the tablet matrix. This pressure causes the tablet to break into smaller fragments, resulting in noticeable tablet disintegration. - Wicking:
Disintegrant with high porosity, such as microcrystalline cellulose (Trade name examples: Avicel, microcel), pull water into the tablet through capillary action. This results in weakening the bonds between particles, leading to successful disintegration. - Gas Generation:
Some disintegrants, such as effervescent agents (e.g., citric acid and sodium bicarbonate), produce gas when they come into contact with water. The gas creates pressure within the tablet, causing it to disintegrate rapidly. - Deformation:
Some disintegrants, such as crospovidone, undergo elastic recovery when exposed to water. This process results in the disruption of the tablet structure, leading to an observed disintegration.
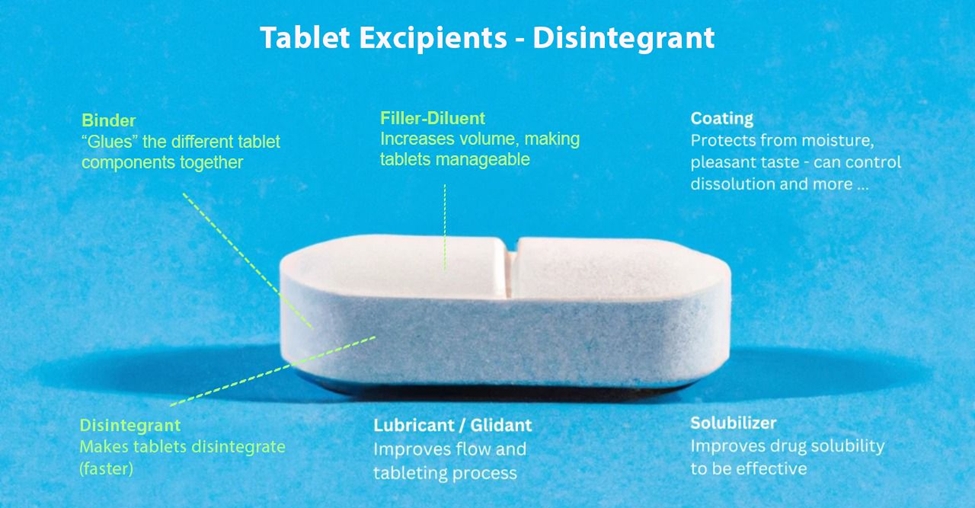
B- Examples of the Commonly Used Disintegrants
Pharmaceutical formulations utilize a variety of disintegrants, each with unique properties and mechanisms of action. Below are some of the most commonly used disintegrants:
1. Croscarmellose sodium:
Croscarmellose sodium belongs to the category of cross-linked polymers of carboxymethylcellulose. Its efficiency is attributed to the rapid penetration of water and its swelling mechanism. It is widely adapted in both immediate and controlled-release dosage forms.
2. Sodium Starch Glycolate:
Sodium starch glycolate is characterized by rapid disintegration and swelling. It is derived from corn or potato starch. It is beneficial in formulations requiring fast drug release.
3. Crospovidone:
Known as cross-linked polyvinylpyrrolidone, crospovidone is a synthetic disintegrant that acts through a combination of deformation and swelling. It is effective even in low concentrations and is compatible with a broad scope of active ingredients.
4. Microcrystalline Cellulose (MCC):
Besides being a filler and binder, it is an effective disintegrant because of its wicking action. It is also used with other disintegrants to improve disintegration efficiency.
5. Effervescent Agents:
These agents, citric acid and sodium bicarbonate, are used when products require rapid dissolution or disintegration. They are frequently used for effervescent tablets and granules.
The primary physical properties relevant to disintegrants describe the product’s particle structure as a dry powder or its structure when in contact with water. These properties may include particle size distribution, water absorption rate, porosity, swelling ratio or swelling index, and whether a gel is formed.
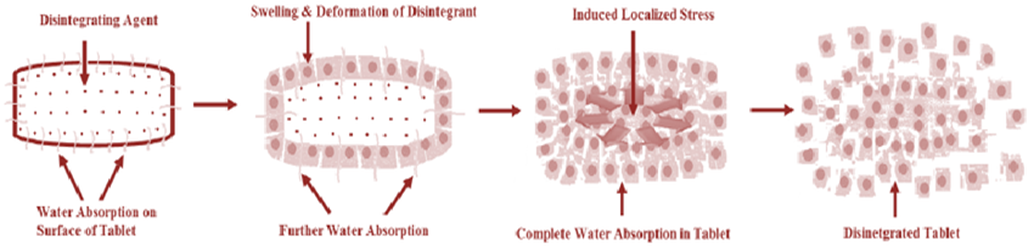
C- Implementations of Disintegrant in Pharmaceutical Formulations
Disintegrants are used in a wide range of pharmaceutical dosage forms, for a certain mechanism requirement regarding the disintegration process, depending on their type. When they come in contact with water or gastric or intestinal fluid, they function by absorbing liquid and swell, dissolve, or form gels.
This results in the dosage form structure rupturing and disintegration, resulting in increased surface area for enhanced dissolution of the API. Some distinguished disintegrants normally exist, which are commonly called super disintegrants, and are effective at lower levels in the final formula, typically less than 10% (w/w). Below are some key implementations:
- Immediate-Release Tablets:
These tablets are designed to release the API rapidly after administration. Disintegrants such as croscarmellose sodium and sodium starch glycolate are commonly used to achieve fast disintegration and drug release. - Orally Disintegrating Tablets (ODTs):
Orally disintegrating tablets are designed to dissolve rapidly in the mouth with no need for the patient to drink water afterwards. Disintegrants such as mannitol and crospovidone are best selected in this case to achieve rapid disintegration, together with flavors to generate a pleasant mouthfeel.
- Controlled-Release Formulations:
Disintegrants here are used in combination with other excipients to achieve a balance between disintegration and sustained drug release. For example, hypromellose (HPMC) can be used as a matrix former, while croscarmellose sodium ensures disintegration in the first phase of the process. - Capsules:
Disintegrants are also used in capsules to ensure the rapid release of the active ingredient. For example, starch and crospovidone can be added to the capsule fill to initiate disintegration, and then the capsule shell dissolves easily afterwards. - Effervescent Tablets:
They rely on disintegrants such as citric acid and sodium bicarbonate to produce gas and facilitate rapid disintegration. These tablets are often used for vitamins, analgesics, and antacids.
Pharmaceutical Lubricants: 4 Critical Benefits of Pharmaceutical Lubricants in Tablet Manufacturing
Challenges in Disintegrant Technology
While disintegrants are essential for drug delivery, they also present several challenges:
- Compatibility with APIs:
They must be compatible with the active ingredient and other excipients in the formula. Incompatibility can lead to chemical reactions, reduced effects, or changes in drug release profiles. - Performance Variability:
Natural disintegrants, such as starch, can exhibit variability in their properties, affecting batch-to-batch consistency. Synthetic disintegrants, while more consistent, may be more expensive, reducing the probability of such an issue. - Formulation Complexity:
The development of complex drug delivery systems, such as multilayer tablets and floating tablets, requires careful selection and optimization of disintegrants to achieve the targeted release profile, which is considered as a unique challenge in pharmaceutical manufacturing nowadays.
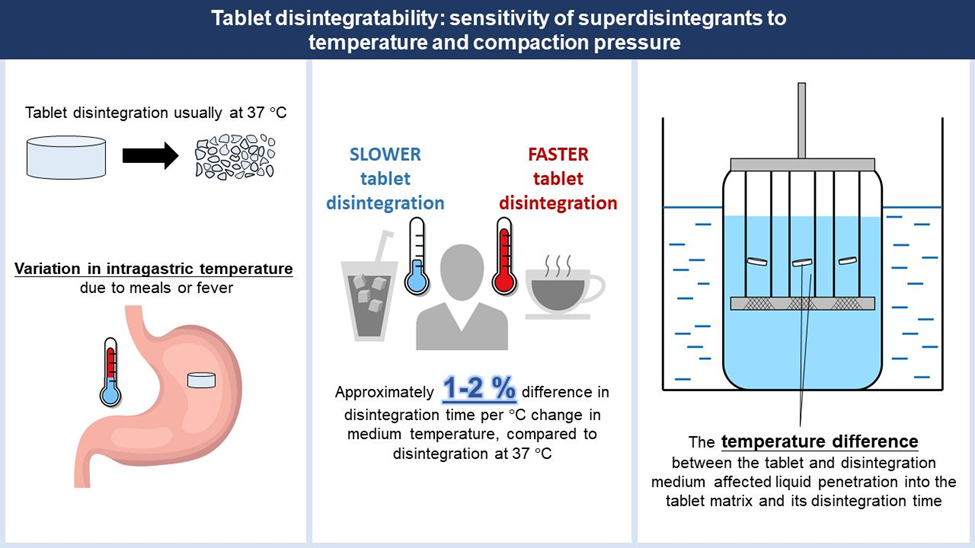
Advancements in Disintegrant Technology
The field of disintegrant technology is continuously evolving, with ongoing research and innovation aimed at improving performance and functionality. Below are some key advancements:
- Co-Processed Excipients:
These are such as Ludipress (a combination of lactose, PVP, and crospovidone), is specifically designed to enhance disintegration efficacy and optimize the formulation process. - Modified-Release Disintegrants:
Researchers are working to enhance those disintegrants with modified-release properties, such as pH-sensitive polymers, to achieve a specific drug release in targeted regions of the gastrointestinal tract. - Green Disintegrants:
With increasing focus on sustainability, researchers are exploring green disintegrants derived from renewable sources, such as plant-based polymers and biodegradable materials.
Pharmaceutical Fillers: 5 Critical Reasons to Choose High-Quality Pharmaceutical Fillers
Conclusion
Pharmaceutical disintegrants are critical excipients that ensure the rapid breakup of solid dosage forms, facilitating the release and absorption of APIs.
From croscarmellose sodium to effervescent agents, disintegrant plays an essential role in optimizing drug delivery systems and enhancing a variety of formulas. However, challenges such as compatibility, variability, and formulation complexity must be addressed to ensure consistent performance.
Novel improvements in disintegrant performance, including co-processed excipients, modified-release disintegrants, and green disintegrants, are driving innovation in the pharmaceutical industry. These advancements are not only improving drug delivery systems but also contributing to the development of more sustainable and patient-friendly products.
As the pharmaceutical industry continues to evolve, the importance of disintegrants will be remarkable. By understanding their function, examples, and implementations, pharmaceutical researchers can optimize formulations to achieve faster, more effective drug delivery and improve patient outcomes.
References: